What is Microscopy?
Ever since the realization that a curved reflective object could magnify distant objects, people were keen on expanding on the technology and began to look without, as well as within. The physics of magnification applied not only to distant objects but close objects as well and scientists quickly turned their attention to the world of the small. Microscopy, as the name implies, is the practice of using microscopes to study objects of microscopic dimensions.
From the invention of the spectacles in the 13-14th centuries to the first recognizable microscope in the 16th century to today’s electron microscopes, technological advancements allowed the curious to view and image the microscopic world in greater detail down to the level of singular atoms.
Microscopy in Forensic Engineering
While the microscope was a ubiquitous tool in the world of forensics practically since its inception, its contribution to the forensic engineering field cannot be understated. In criminal forensics, microscopes are widely used to identify and classify objects of interest such as fibers, tool marks, fluid spatter, impressions, and many more. The techniques specialists rely on are finely defined yet flexible such that other fields of study can use the same techniques or variations thereof for their needs.
Engineers have relied on the optical microscope in order to discern surface features on fracture surfaces not readily visible to the naked eye. These surface features tell the history of how a particular object failed. Be it a chronic event such as a fatigue fracture or a single overload of a brittle fracture. There are as numerous fracture modes as the books written on the subject and in the interest of brevity, will not be discussed here. Suffice it to say, that studying the fracture surfaces often clarifies the loading conditions necessary to produce such a fracture and accompanying features and allows the experts to form opinions as to the cause of failure defensible in court.
Example 1: Domestic Water Leak
In a particular instance, VERTEX was requested to examine a domestic water leak that damaged multiple levels of the home and the contents within. The copper pipe section in question was already replaced with a new section patched with repair couplings by the time the inspection took place and what was reported as the original, damaged pipe was presented separately. The presented section appeared to be dated consistently with the rest of the piping in the home. However, upon visual examination alone, it could not be determined with certainty that it was the section that was originally present. VERTEX proceeded to remove the repaired section taking care to preserve the cuts hidden underneath the repair couplings. In a laboratory setting, VERTEX removed the repair couplings and compared the cut surfaces of the existing pipes and the presented section of the pipe. VERTEX found that the cut surface features of the original piping did not match the cut surface features of the presented section concluding that the presented section did not represent what was originally installed and caused the water damage. Through the use of microscopy, VERTEX clearly identified and documented the cut surfaces of the original piping and the presented section for reporting and presented the findings to the client.
Example 2: “Catastrophic” Separation of Rotating Assembly Part in HVAC System
In another instance, VERTEX was requested to investigate a “catastrophic” separation of a rotating assembly part of a building’s HVAC system and determine the cause. It was alleged that the separation occurred suddenly without any warning. Through the use of a macro lens on a digital camera, VERTEX was able to determine, in the field, that the separation was a time-related event due to the presence of fracture surface features characteristic of cyclic loading that resulted in a growth of a fatigue fracture. This eliminated a costly need for a laboratory examination saving the client’s resources while delivering a valuable work product.
Stereo Microscopes
Commonly used in forensic laboratory work, stereo microscopes are low power microscopes that provide three-dimensional views of specimens visible to the naked eye. Stereo microscopes utilize binocular eyepieces and are often enhanced with digital features. Modern optical microscopes often feature digitized controls and digital optical sensors that replace the eyepieces. These digital microscopes offer greater analysis capabilities by comparison, such as on-screen measurements, feature enumeration, three-dimensional reconstruction of an object, and stitching and tiling of images.
Microscopes are not limited to magnification of visible light and technology exists that can resolve features of nanoscale.
What is a Scanning Electron Microscope (SEM)?
A scanning electron microscope, or an SEM, is like the name implies, a microscope that relies on electrons rather than the visible light to resolve an image of the object under magnification. Unlike an optical microscope which relies on the reflected visible light from an object for magnification, an SEM uses an electron beam. At a high level, an SEM produces a beam of electrons that interact with the surface under examination to produce an image. As the beam can be finely controlled, the final image can resolve features nanometers in scale. This is an extremely powerful feature, as unlike reflected light which can scatter and necessarily interacts with optics, the final SEM image is extremely detailed and expose the features of the examined object with little distortion under high magnification.
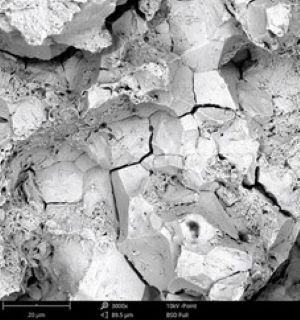
Source: nanoScience Instruments
In addition, due to the physics of the electron interaction with materials, an engineer may query the information collected by the SEM’s sensors to identify the material on the elemental level in a process referred to as energy dispersive spectroscopy, or EDS.
For example, an engineer may have specified a specific brass alloy to be used in a fitting for an industrial application. That fitting failed and resulted in a release of a hazardous gas leading to a fire. Upon examination by the expert using an SEM with EDS capability, the expert was able to identify that the material in the fitting as manufactured did not adhere to the specifications set by the designing engineer. Through this method, the expert was able to map the elements and visually represent the defect at and near the fracture surface to conclusively show the material defect which lead to the accident.
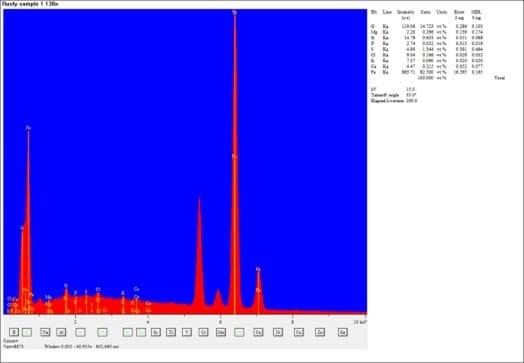
Source: ScienceDirect
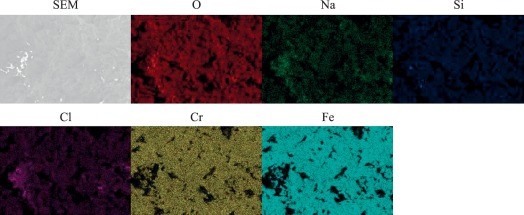
Source: ScienceDirect
In another example, a marine engine mesh strainer was submitted as defective due to corrosion which caused parts of the strainer to be ingested by the motor resulting in damage due to cooling passage blockages. Through bulk examination using EDS, the expert was able to identify that the material with which the strainer was manufactured was not compatible with the salt water in which the marine vessel operated and not consistent with the specifications set by the designing engineer.
There are databases that exist which specify the elemental composition of standardized alloys such as stainless steel 300 series, or aluminum 6000 and 7000 series. Without delving into detail of the chemistry and physical properties of these material classes, it is sufficient to note that each have a preferred application within the industry ranging from common household fasteners to aircraft skin and structure. A manufacturing defect or a misapplication of the material can have dire consequences and the use of an SEM with EDS is a powerful tool in the forensics industry to determine, with confidence, whether an accident was a result of a material defect.
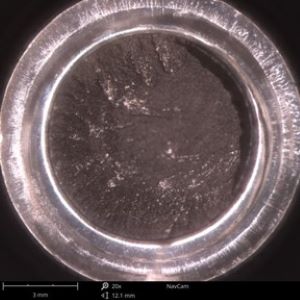
Source: nanoScience Instruments
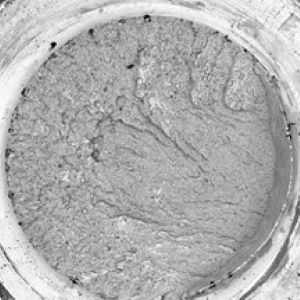
Source: nanoScience Instruments
In sum, an SEM allows for much greater flexibility in examining a surface compared to using an optical microscope and can produce data on the material composition. Whether it be examining minutely small features or nano-sized inclusions in a material, the SEM is capable of delivering clear visuals and detailed composition results that aid the forensic engineer in his duty to determine the cause of loss. Utilizing these tools early in the investigation can guide the direction of the process and save the client valuable resources.
To learn more about VERTEX’s Forensic Engineering services or to speak with a Forensic Expert, call 888.298.5162 or submit an inquiry.