Right now, the COVID-19 crisis is taking a toll on all industries and the construction sector is no exception. Still, even while construction companies are reeling from project shutdowns, it is not too early to look forward. When the dust settles and the pandemic subsides, companies will be scrambling to get back to work – any way they can. The urgency is likely to spur players in both public and private sectors to look at the lessons learned in providing temporary medical facilities and housing for those afflicted by the virus: specifically, the use of prefabricated and or modular buildings.
For those in the insurance and surety world, now is the time to prepare for what could become a race to capitalize on a rise in demand for modular construction projects. Here, we offer a few key factors to contemplate when considering underwriting future modular projects and hopefully, before adjusting claims related to them.
1. Be clear on the definition of “experienced”
In a post-pandemic or quasi-pandemic world, modular construction on a grander scale could provide a longer-term solution to the needs of growing populations and a way to prepare for surges or future pandemics. Inevitably then, developers, designers and contractors not “schooled” or “experienced” with modular construction are likely to see this model as one way to quickly rebuild their businesses.
The nuances of modular construction projects are somewhat atypical when compared to traditional general contracting methods: there is a heightened need for planning and “measuring twice to cut once.”
Simply put: contractors who have successfully built multiple modular projects as a general contractor or have operated as a sole source modular constructer/installer are the most qualified.
2. Understand the logistics required to support concurrent work
A key benefit of modular construction is that it can save time. One example of how that works is that modular units can be constructed at the same time (concurrently) as the site is being prepared. While this can be true, logistics plays a much bigger role in making that possible than it does in traditional projects and therefore needs to be carefully managed to avoid slippage.
Key logistical factors to understand:
- trucking time and the costs of getting the units to the site,
- border crossings (customs) if international travel is required on the route,
- limitations of highways and access roads,
- storage and marshalling yards (rental) on or offsite for pre-setting preparations,
- traffic patterns near the site,
- crane setup, relocation time, and the impact of multiple crane “pick” points – all of which may limit what site work can be achieved concurrently.
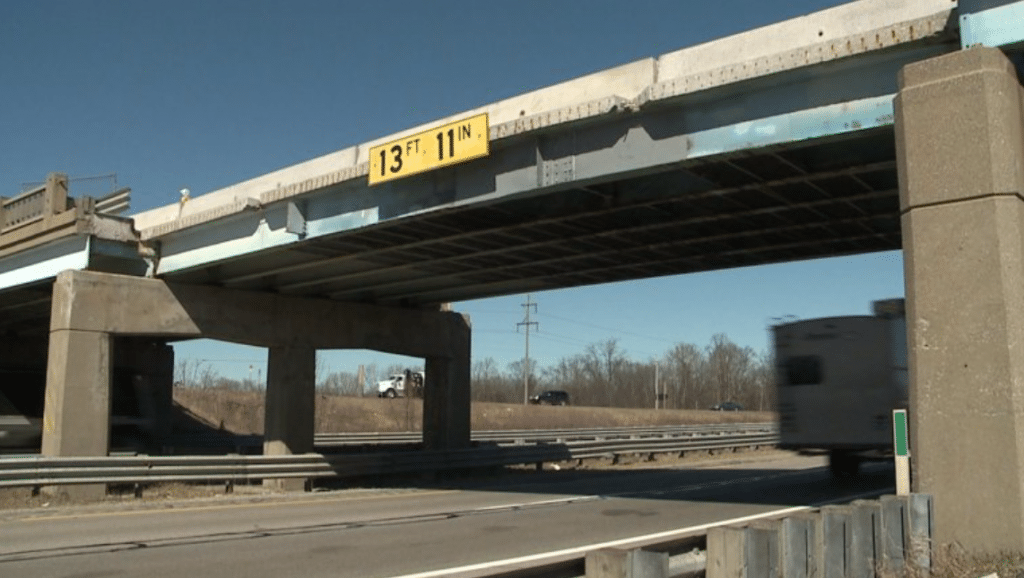
3. Protect work-in-progress from the elements
Prefabricated “boxes” that ultimately will be stacked to construct a multi-story building may have interior finishes that could be exposed to the elements during transit, storage, the erection process, and after they have been set. Sheet-rocked walls with insulation, casework, and mechanical equipment are also at risk of exposure and potential mold growth if not well protected.
Design details need to incorporate temporary weather protection that can reduce the risk of water damage at all stages of the project; the timing and size of a modular or traditional roof system can play a major role in determining the robustness required for temporary protection.
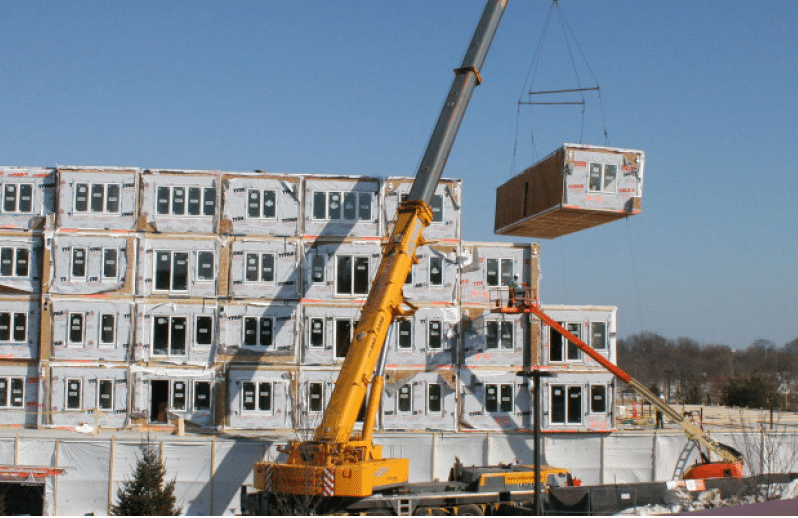
4. There’s no such thing as too much coordination between the trades
Successful coordination on a modular project requires that all of the major trades, (typically mechanical, electrical and plumbing contractors) be involved early in the design phase.
Why is this so important? The design team needs to fully understand
- what tradesmen need to connect the parts and pieces of the “boxes” in the field,
- how the work will be done and
- to what level the units need to be finished before a particular trade begins work in order to minimize potential rework.
Coordination between the “box” manufacturer and these trades is also necessary if they intend to install their equipment during the production stage. Since the factory could be in another state or country, special attention to ensure that the codes required at the final location are being followed is essential (see #6).
5. Tolerance variance must align with specification standards for acceptability
One unique challenge of modular construction projects is caused by the reality that tolerances in building materials vary significantly. These variances create issues when units are finally brought together and walls or floors don’t align properly.
If a contractor does not have plans for dealing with these tolerance variances challenges will arise, especially when strict specifications dictate acceptability.
6. A clearly defined and developed Quality Assurance/Quality Control (QA/QC) plan is critical
Construction in a “controlled environment” does not necessarily generate a better product: what happens before the units arrive on site needs to be monitored closely – just as it would be if the work was taking place in the field. This will ensure that the work that happens at the factory will be acceptable once the product arrives in the field.
It is essential that all parties understand when and how inspections will take place in the factory and in the field. A few nuances of note:
- Rework of finished spaces in most cases will not be easy and will undoubtedly cause delays.
- Of particular concern are the code enforcement inspections that need to meet all requirements of the project location, not the factory location.
- Licensed local inspectors for the given project location may need to be hired to travel to the factory site to review the various levels of work from rough-in to finish fixtures for all the units being constructed. These inspections need to be figured as part of the assembly line process on the schedule to avoid production slowdowns.
7. Remember the 5 P’s (Prior Planning Prevents Poor Performance)
The single most important question to ask: Was every aspect of pre-planning exhausted prior to issuing the plans for construction?
The importance of pre-design interviews and the design development phase of modular construction cannot be overstated. Nor can ensuring that all parties understand the limitations on future changes once the construction begins.
When design and planning have been done to the nth degree, and everyone understands that even the smallest change will quickly erase any benefits of time or cost that a modular delivery model should ultimately provide, the project will begin on the right path.
What Works for Traditional Construction May Not Apply to Modular Projects
Capitalizing on the benefits of modular means exploiting controlled construction, quality and less labor to achieve savings in time and cost through repeatable units. The current pandemic has shown both successful and not so successful uses of modular construction thus far, and it is inevitable that both public and private institutions will ultimately use modular for new permanent facilities or for future emergency facilities.
In the surety claims world, we often deal with projects that are behind schedule and over budget. So, we might think that there would be no difference when underwriting or adjusting a claim related to a modular construction project.
Not so fast.
While the content here is by no means exhaustive, it highlights some of the major considerations for sureties when underwriting or adjusting these types of performance bond claims. The key takeaway: the ways in which common issues, like schedule delays and cost overruns, arise and how to avoid them will be different when dealing with modular construction projects vs. more traditional construction.
With that understanding in mind, surety and insurance strategies can be designed and executed to suit the unique requirements of the modular construction method and delivery model for the long term.
For more information on modular construction projects and surety and insurance, please contact Jonathan Hahn or submit an inquiry.