How Popular is Fuel Oil for Residential Heating and Why?
Despite recent trends toward less reliance on fossil fuels, fuel oil continues to be popular for heating residences in the Northeastern region of the United States. According to the U.S. Energy Information Administration, in 2020, 4,093,000 of 123,053,000 housing units (3.3 percent) in the U.S. utilized fuel oil or kerosene as fuel for space heating equipment[1]. However, that same year, 4,070,000 of 21,920,000 housing units (18.5 percent) in the Northeast utilized fuel oil or kerosene for space heating equipment. Much of the concentration of fuel oil heating in the Northeast is associated with fuel oil infrastructure developed over the last 100 years as fuel oil heating emerged as a preferred choice over burning wood and coal, referenced in the timeline below.
Industrial Revolution Fuels Change
- 1775: Discovery of electricity
- 1831: Invention of electric motor
- 1849: Invention of coal-fired furnace for home heating
- 1859: World’s first oil well drilled, Titusville, PA
- 1863: Invention of cast iron radiators
- 1885: US burns more coal than wood for home heating
- 1925: Introduction of fuel oil burner to home heating
- 1935: First Coal-fired, forced-air furnace introduced
- 1938: Oil and Gas-fired, forced-air furnaces introduced
- 2024: After more than 85 years later, basic design of fuel oil furnaces remains unchanged
Fuel oil for residential heating continues to be a viable option in areas where natural gas pipelines do not exist, when dependence on a utility company is not desired, for desired increased safety of using a liquid fuel over a gas fuel, and in the case of dual-fuel commercial boilers, having the ability to select fuels based on costs and utility rate reductions, associated with natural gas interruption capabilities.
Oil-fired Furnaces vs Oil-fired Boilers: Different Ways to Heat a Home
What is an Oil-fired Boiler?
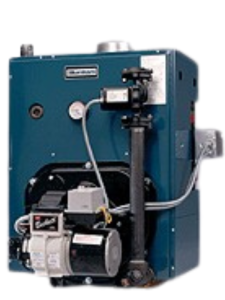
An oil-fired boiler is that component of home heating system that heats water to provide warmth, using oil as a fuel source.
What is an Oil Furnace?
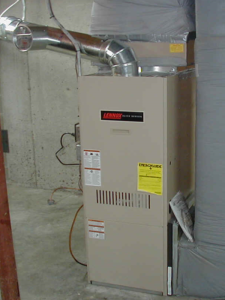
An oil-fired furnace is that component of a home heating system that heats air to provide warmth, using oil as a fuel source.
The Primary Components of an Oil-fired Furnace
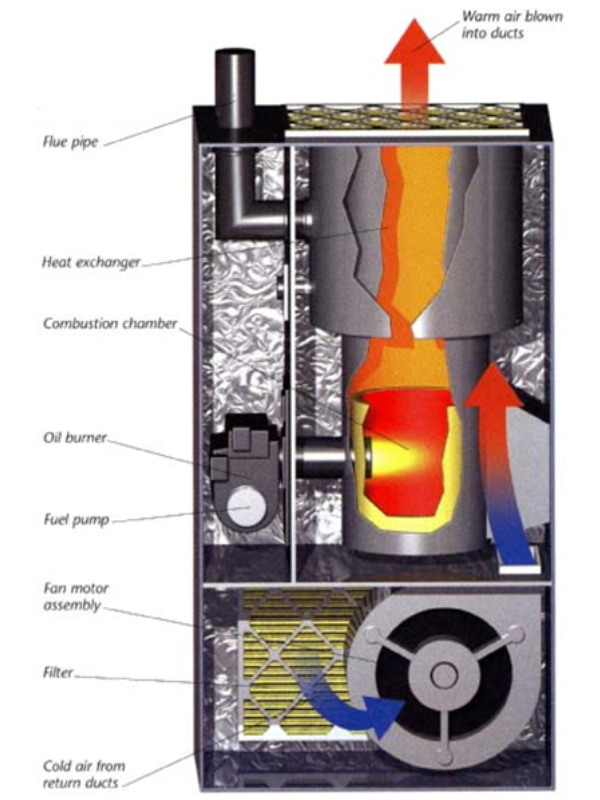
The Primary Components of an Oil-fired Boiler
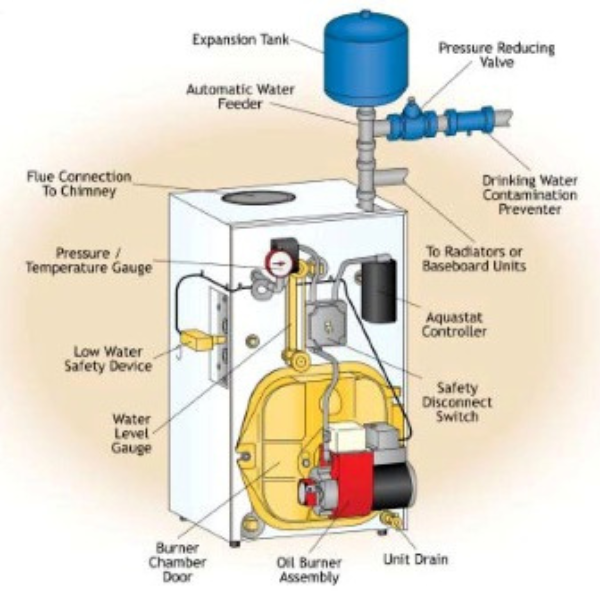
Oil Burners: The “Heart” of Oil-fired Furnaces and Boilers
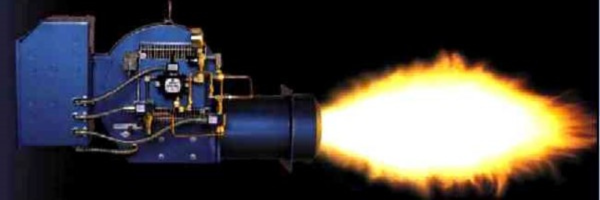
Oil burners convert fuel oil into heat energy. Burner designs for furnaces and boilers are similar in concept, varying by complexity.
What are the Key Components of Oil Burners and What do they do?
- An electric motor that drives the fan and fuel pump.
- The fan flows air to the burner’s air tube to support combustion.
- The oil pump draws fuel from the tank and delivers it to the nozzle.
- The ignition transformer produces a high-voltage spark that provides enough heat to vaporize the atomized oil from the nozzle and achieve ignition.
- The igniter assembly contains the electrodes that position the spark for to achieve optimal combustion.
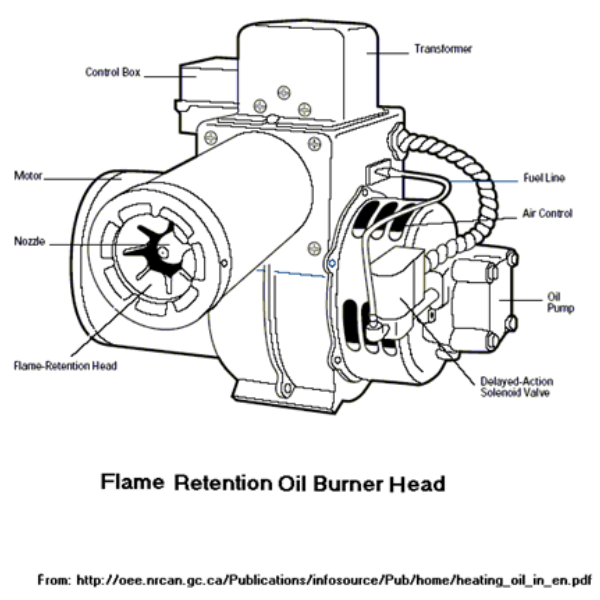
How Does an Oil Burner Work?
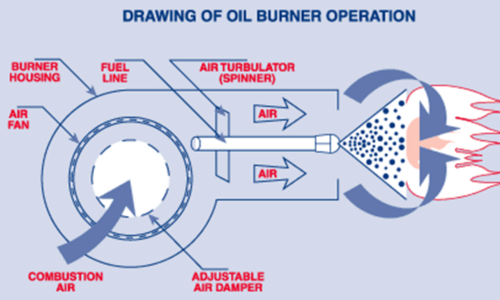
Nozzles: The “Heart” of Oil Burners
Heating fuel oil in liquid form must be converted into vapor and mixed with air before it can burn. When the oil from the storage tank reaches the burner’s nozzle, it is broken into small droplets. This process is called atomization. These droplets are mixed with air and then ignited by the burner.
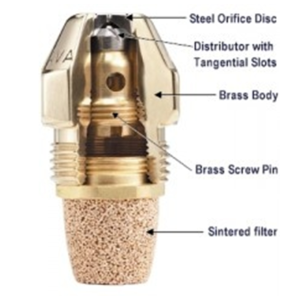
The function of the nozzle is to atomize the fuel oil. Atomization involves the separation of the liquid fuel oil into small droplets. The atomization process begins with forcing the oil through a set of slots.
Nozzles and Atomization
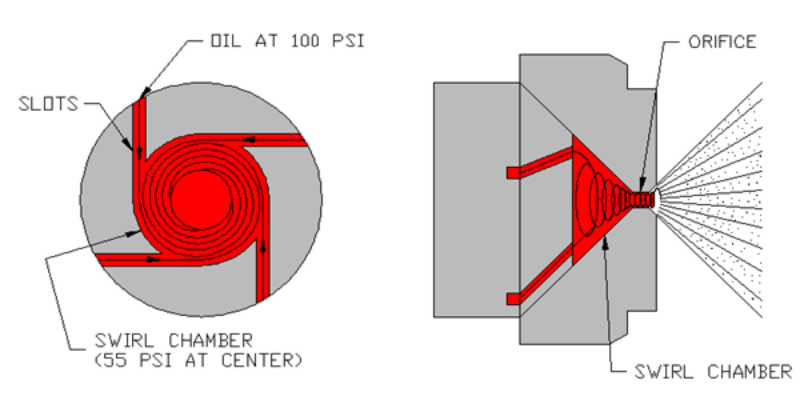
Slots are cut tangentially into a swirl chamber. Pressurized streams of fuel oil entering the swirl chamber create high velocity rotation within the chamber. The velocity of rotation increases as the liquid approaches the center of the swirl chamber. The velocity of rotation at the center is high resulting in an air core created at the center of the vortex. The fuel oil then extends into the orifice in the form of a rapidly rotating tube of oil, leaving an air core in the center. As this tube of oil rotates, it pushes outward against the walls of the orifice due to the centrifugal force developed, resulting in small (atomized) droplets that can be ignited in the presence of oxygen.
Analogy: A Coin Donation Funnel
To visualize, consider a coin donation funnel, which is analogous in function to a swirl chamber as shown below. As coins are deposited, they enter the top of the funnel, which is the funnel’s highest and widest section. Set into a rolling motion under gravity conditions, the coins roll along the decreasing circumference of the funnel walls and descend in a swirling fashion. Following a circular trajectory that decreases, the coins gain speed and momentum as they approach the bottom of the funnel. Upon exiting the funnel at high speed, the coins are hurled in a direction away from the center of the funnel. In a similar manner, a nozzle releases small streams of fuel oil outward from the center of the swirl chamber at high speed, resulting in the formation of small droplets. This type of conversion from a liquid to a vapor is referred to as atomization.
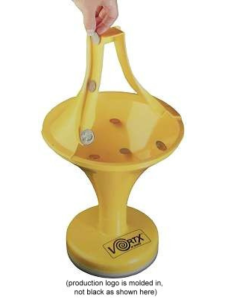
What is a Puffback?
During the heating season, puffbacks in furnaces and boilers are often investigated by the VERTEX team. A puffback is an explosion of unburned oil in the combustion chamber of an oil-fired boiler or furnace. A puffback may:
- Damage the furnace or boiler itself, depending on the quantity of oil ignited.
- Damage the flue vent piping.
- Distribute soot throughout the building.
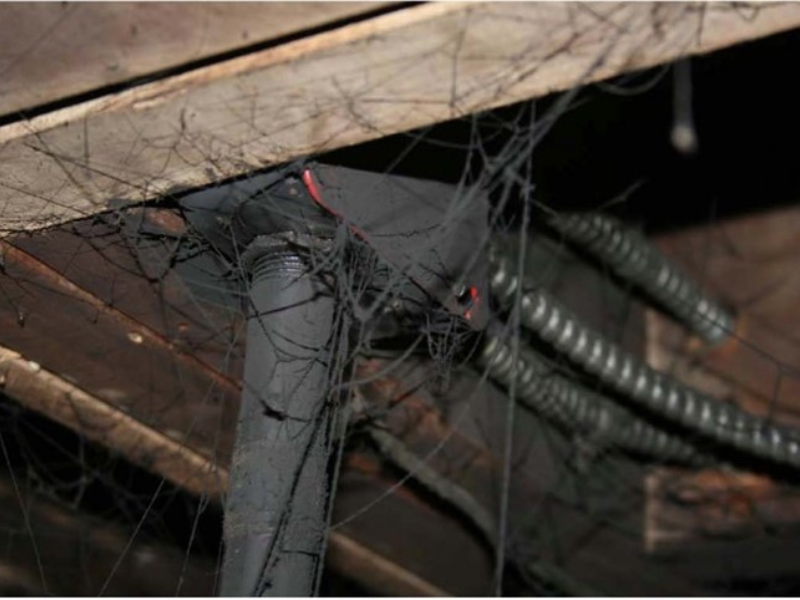
Featured Above: Soot deposits on surfaces of the boiler room including the discolored cobwebs shown.
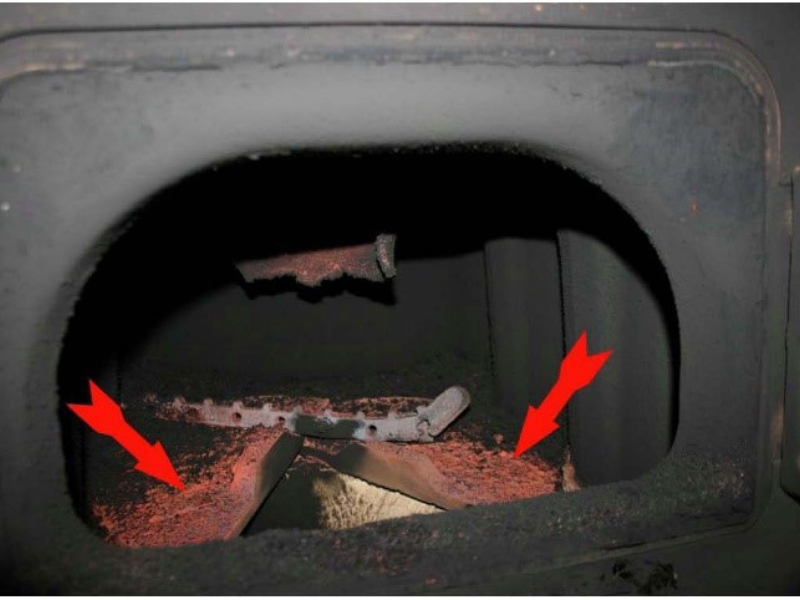
Featured above: Arrows point to dislodged refractory materials covered in part with soot, indicative that a puffback took place.
Preventative maintenance is the key to reducing the likelihood of a puffback occurring. Annual servicing of the furnace or boiler by a service provider qualified by the equipment manufacturer is recommended. During servicing, the service provider will replace air and fuel filters, clean flue pipes, and check system operation, including combustion performance. This includes replacing the burner nozzle, which if not maintained, can cause, or contribute to the cause of a puffback.
Interested in learning more?
VERTEX’s team of mechanical engineers have expertise with all aspects of Furnace and Boiler design, operation, installation, and commissioning. We are available to review your Furnace and Boiler system and help you identify issues which could lead to system failures. For more information, please contact me at jimperatore@vertexeng.com or The Vertex Companies, LLC at vertexeng.com/contact-us.
References:
[1] Data source: U.S. Energy Information Administration, Office of Energy Demand and Integrated Statistics, Form EIA-457A of the 2020 Residential Energy Consumption Survey.