In previous posts on schedule analysis methodologies, we’ve discussed the role of delay analysis methods in calculating the effect of a change on a project’s performance period. One of the most commonly encountered methods is “As-Planned versus As-Built.” In this post, we describe the method and walk through the general procedure for performing an As-Planned versus As-Built Analysis, and discuss some strengths and weaknesses of this delay analysis method from a construction delay claim perspective.
What is the As-Planned versus As-Built Method?
The As-Planned versus As-Built Method simply compares what actually happened to what was supposed to happen. It measures the activities of the baseline or other planned schedule against that of the as-built schedule or schedule updates to identify encountered delays. When using this method, it is important that delays are measured by the differences between the as-built actual dates and the late dates in the as-planned schedule as opposed to the early dates. The late dates reflect when available float for the activity is exhausted and thus when the activity becomes critical.
The As-Planned versus As-Built methodology is very popular among contractors and claims analysts alike. In a 2006 study, more than 60 organizations made up of contractors and construction consultants reported using the As-Planned versus As-Built Method more than any other delay analysis technique. They also ranked it as the most effective method in terms of success. This result is especially surprising given that many in the industry view the method as being one that is most prone to challenge by the opposition.
Strengths of the As-Planned versus As-Built Method
A contractor or claims analyst has a number of things to consider when selecting which delay analysis methodology to employ. Sometimes, a certain method will be explicitly called for in the contract documents. More often, however, there is flexibility in deciding what method is best for the given dispute. In these situations, the person preparing the claim should consider what method best supports their opinions of the issue, based on the nature of the dispute and the available documentation.
Even in the most straightforward disputes, overly complex analysis can diminish the chances of recovery. If a delay analysis is too complicated to follow, then the evaluator will not trust its findings. One of the greatest strengths of the As-Planned versus As-Built Method is that it is very easy to understand and thus appealing to those presenting to an inexperienced audience.
Figure 1 – Graphical Depiction of an As-Planned vs. As-Built Analysis
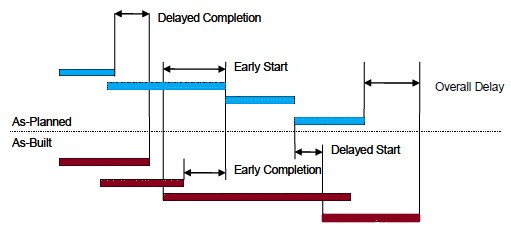
Source: AACE International Recommended Practice No 29R-03 – Forensic Schedule Analysis, AACE International, Morgantown, WV, 2011
With the simplicity of the method comes the added benefit of low-resource requirements. Because the method is less intensive than other methods, the time required to prepare the analysis is typically significantly less than that of other more complex methods. And in situations where an outside consultant is being used, this translates into lower costs for the client. The simplicity and ease of use are likely the primary factors behind the overwhelming popularity of the method by claimants.
Again, in the previously mentioned survey, construction contractors and claims consultants ranked inadequate project record documentation as the most frequently encountered obstacle to the effective use of certain delay analysis methods. Ideally, the effect of a delay impact on the schedule is measured at the time it occurs. To do so, the project schedule must be properly maintained by regularly updating it to reflect the actual start and finish dates, reassessed activity durations, modified activity relationships, etc. Oftentimes, contractors fail to adequately update the project schedule thus precluding the use of some of the more technical delay analysis methodologies. In these cases, the As-Planned versus As-Built Method is an attractive option, as it does not require contemporaneous updates.
Weaknesses of the As-Planned versus As-Built Method
All that said, while the As-Planned versus As-Built Method is simple and inexpensive to implement, and overcomes limitations with available documentation, it does have weaknesses that should be considered when evaluating its use. For example, the method is not well-suited to determining delay causation when a project is complex, spans longer durations, or is built in a manner that significantly deviates from the planned sequence. Additionally, the method is not typically appropriate for projects that include near-critical paths that experienced delay, as the method cannot consider shifts in the critical path over time.
Figure 2 – Graphical Depiction of a Segmented As-Planned vs. As-Built Analysis (Windows Analysis)
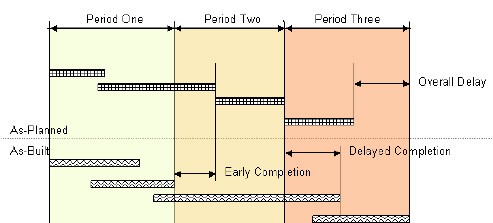
Source: AACE International Recommended Practice No 29R-03 – Forensic Schedule Analysis, AACE International, Morgantown, WV, 2011
Another limitation of the method is its failure to consider concurrent delays. The As-Planned versus As-Built Method will not typically depict these critical considerations. Special attention to documenting concurrent impacts or known pacing events when performing the analysis is critical.
Ultimately, while a common delay analysis technique, the As-Planned versus As-Built analysis may or may not be suitable for your given situation. The above provides only a brief discussion of the method and its limitations.
To learn more about VERTEX’s Construction Claims Consulting services or to speak with a Construction Claims Expert, call 646.553.3500 or submit an inquiry.
Reference
- Ndekugri, Issaka, et al. “Delay Analysis within Construction Contracting Organizations.” Journal of Construction Engineering and Management, vol. 134, no. 9, 2008, pp. 692–700., doi:10.1061/(asce)0733-9364(2008)134:9(692).