Water intrusion through fenestrations can result in costly repairs that, if identified prior to completion of a building’s construction, can be avoided. Water penetration may occur due to improper installation of the window or its associated sealants, a defect in the window’s construction at the time of manufacture, or by simply just shipping the product to the job site. Therefore, for owners to be confident that openings in the building envelope will meet or exceed design requirements, it is recommended that water penetration resistance testing be performed during the construction process to identify and correct any deficiencies. Such deficiencies are more easily resolved during construction, prior to significant damage occurring – such as mold and associated poor indoor air quality – and disruption of the building occupants. While some may consider the testing to be an unnecessary additional project expense, the cost of testing is small compared to the potential costs down the road.
While the project specifications may include a requirement for field testing of windows, it is in the best interest of owners and contractors to include spray testing representative samples of installed windows in the event the specifications do not have such a requirement.
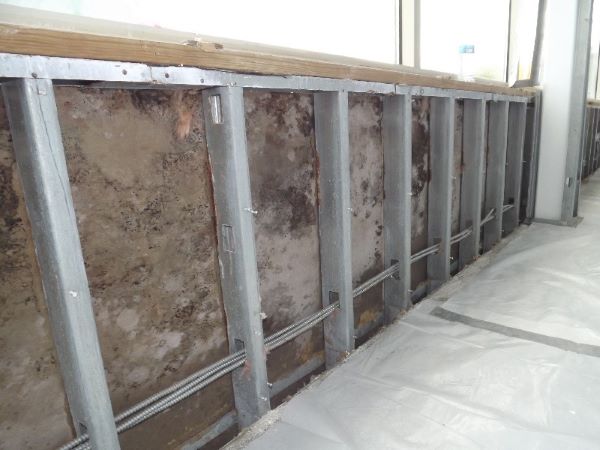
What is Water Penetration Testing?
Since laboratory tests that are performed by manufacturers can only simulate field conditions which may not truly reflect actual conditions, a water penetration field test (sometimes referred to as a spray test) is a quality assurance process to verify and document the proper installation and performance of the installed products, and absence of construction defects of the installed product.
There are several industry standard test methods for conducting field spray tests to determine water penetration resistance through the assemblies and ensure compliance with performance criteria. The Architectural Manufacturers Association (AAMA) and American Standard for Testing and Materials (ASTM) both have specific protocols for spray tests, depending on certain variables, such as the type of fenestration product – whether it be a storefront, curtain wall, or individual operable and inoperable window assemblies – the purpose of the test, and the environmental conditions to be simulated.
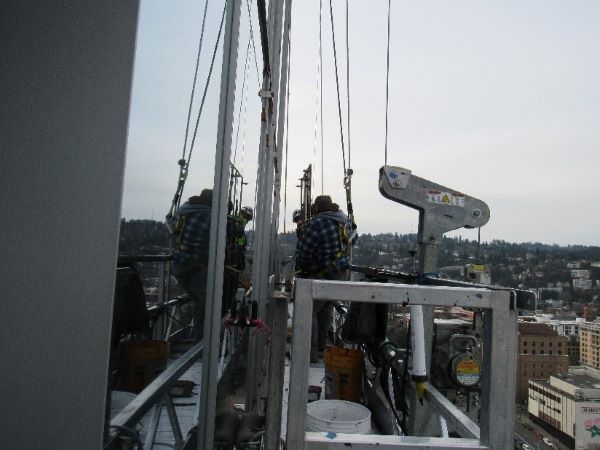
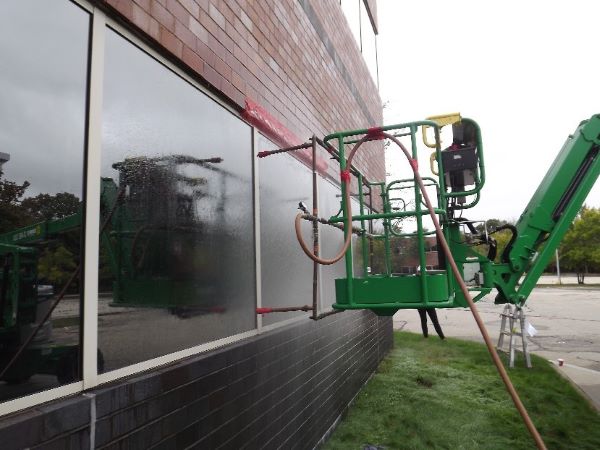
ASTM E1105 (Standard Test Method for Field Determination of Water Penetration of Installed Exterior Windows, Skylights, Doors, and Curtain Walls by Uniform or Cyclic Static Air Pressure Difference) provides the standard procedure to test the installed fenestration product for resistance to water penetration. This method may also be used to test the joints between the assemblies (i.e., a mullion) and the adjacent facade. In general, a sealed “chamber” encompassing the interior of the test area is reduced in pressure while the exterior pressure remains static at atmospheric pressure. The negative air pressure, combined with the spray test, is intended to replicate wind-driven drain. The pressure differential between the interior and exterior of the window may be constant, or it may be cycled to simulate conditions similar to wind-driven rain. A spray rack consisting of multiple, equally-spaced nozzles calibrated to a minimum flow of 5 gallons per square foot per hour is utilized on the outside of the specimen to uniformly distribute water, and various pressure measurements and observations are recorded throughout the test. It should be noted that it is beneficial to conduct the tests prior to the installation of interior finishes to easily identify leaks.
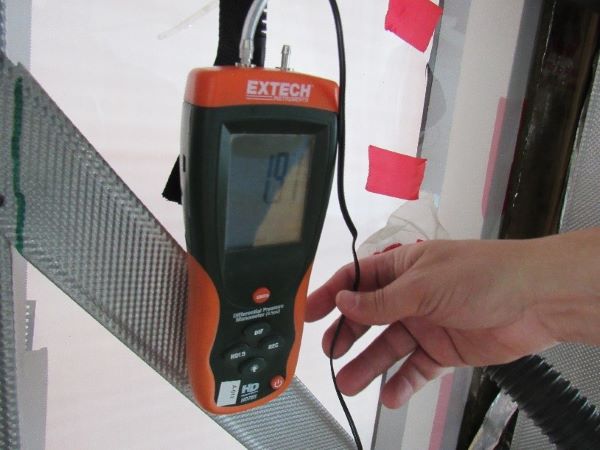
Personnel conducting the tests should be properly trained so there is a clear understanding of the purpose and procedures. Documentation of the test is also key and should include, among other things, a description of the specimen, test parameters, environmental conditions, a summary of the results (including specific information concerning the location of any observed leaks), and any deviations from the established protocol. The aforementioned information is then summarized in a report which is critical in the event deficiencies are identified and a remedial effort is required.
Benefits of Water Penetration Testing
The benefits of spray tests far outweigh the possible adverse consequences. While not required by building codes, water penetration testing is usually performed per contractual requirements of the owner. However, in the absence of contractual requirements, some contractors choose to retain a qualified firm to conduct spray tests to reduce the possibility of an associated construction defect claims following completion of construction.
As mentioned before, early identification of potential water intrusion resulting from construction or product defects is vital to ensure the adequate performance of the overall building envelope and properly conducted spray tests are an excellent means of determining whether the products were installed as specified and will perform as intended. Avoiding post-construction water intrusion issues can only benefit the owner by reducing the possibility of operational interruptions, expensive and intrusive repairs, and litigation expenses in the future.
How Can VERTEX Help?
The VERTEX team of engineering and architectural professionals have the experience and expertise to facilitate water penetration tests, interpret the results, and if needed, develop remedial strategies and their associated cost estimates. In addition, in the event water intrusion has already occurred and a remedial plan is needed to address restoration or indoor air quality issues, VERTEX also has a staff of specialists, including Certified Industrial Hygienists (CIHs), that can help bring your building back to proper operating conditions.
To learn more about VERTEX’s Forensic Engineering and Forensic Architecture services or to speak with a Forensic Expert, call 888.298.5162 or submit an inquiry.