Key Factors Contributing to Mold Growth in New Construction
Mold is a common concern in older homes and commercial structures, but what surprises many is its presence in new construction, sometimes even before the final finishes are applied. In this blog, we delve into the conditions necessary for mold growth in indoor environments, exploring the crucial factors that mold relies on. Furthermore, we’ll discuss effective strategies for safeguarding construction materials during storage and transportation, as well as proactive measures to prevent mold growth in new buildings. Mold’s impact on project costs, schedules, and property value cannot be underestimated, making it essential for builders to be well-informed about prevention methods.
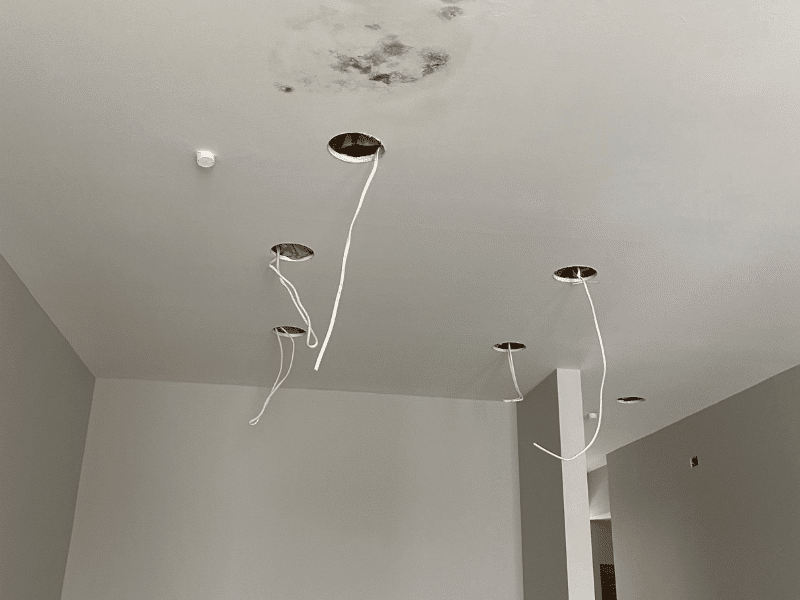
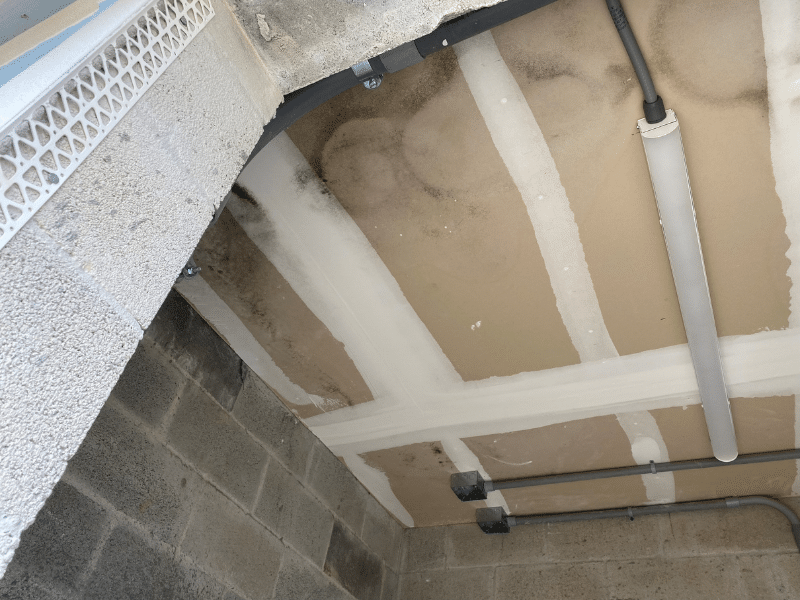
Photos courtesy of Nacole Caputo with VERTEX
Understanding the Conditions for Mold Growth in Indoor Environments
While it is not uncommon to find mold in older homes and commercial structures, did you know that it is also not uncommon to find mold in new construction? Even before the finishes have been completed? How can this be possible?
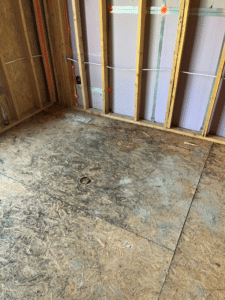
Mold on newly installed flooring. Photograph courtesy of Michael Cope with VERTEX
Mold and mold spores are present in all outdoor environments and in most indoor environments (exceptions might be clean rooms, surgical rooms, etc.) Mold spores in the indoor environment don’t always mean that mold will grow indoors. Mold needs the right environment to grow and proliferate indoors and the three main factors that mold needs to grow are:
- An organic food source with cellulose, such as wood, paper, rock wool insulation, and porous fabrics
- Moisture content in wood and drywall. Wood construction materials with a moisture content in excess of approximately 16-19% are considered to have elevated moisture content (all wood has some moisture content). “Dry” lumber, as defined by the American Softwood Lumber Standard, has a maximum moisture content of 19%.[1] Drywall is considered to have elevated moisture content if it contains in excess of approximately 5-12% moisture, although this can vary from region to region.
- Excess humidity in the indoor environment. The American Society of Heating, Refrigerating and Air-Conditioning Engineers (ASHRAE) 62.1[2] guidance recommends maintaining an indoor relative humidity level of less than 60% or less.
We know that mold spores are present in most indoor environments. To be clear, the Author of this blog is not a construction expert or engineer, but rather a Certified Industrial Hygienist with The VERTEX Companies and the content herein is based on past projects and observations that I have seen or been involved with over the past several years related to mold in pre-installed construction materials. There are several ways in which mold or moisture can intrude into new construction and examples of these include:
- poor foundation seals
- poorly installed roofs, windows, and doors or other openings
- improper grading
- lack of or poorly installed vapor barriers
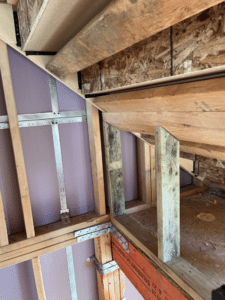
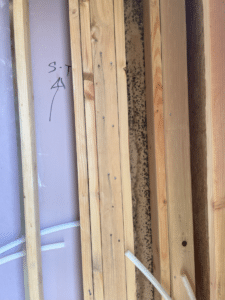
Mold growth in new construction, multi-family housing. Photos courtesy of Zack Westfall with VERTEX.
But one thing that is often overlooked is moisture or mold associated with building materials that haven’t been installed yet, such as drywall and framing members, that are transported and stored on site until installation.
An important factor in preventing the introduction of moisture or mold in a new building is the way in which building materials are stored, especially in climates that are humid or prone to rain and snow. Sometimes, General Contractors or Construction Companies are in a rush to get a structure built over the Fall and Winter so they are ready for occupancy in the Spring and Summer. Sometimes, there is a construction schedule that must be maintained despite challenging environmental elements. Either way, improper storage of construction materials on site that get exposed to the elements is a common way to introduce mold into a new building.
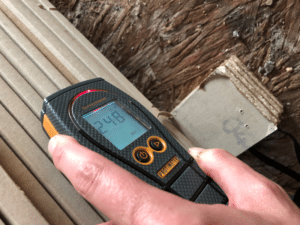
Elevated moisture content in stored drywall. Photographs courtesy of Nacole Caputo with VERTEX
Effective Strategies for Protecting Building Materials during Storage and Transport
Storage off-site and transport of building materials to the site can also be a source of excess moisture that, if installed, can induce mold growth. Off-site storage and transport of building products is often out of the control of a General Contractor or installation Subcontractor, so it is important to know where and how the materials were stored and transported prior to acceptance of deliveries. Were they stored in a humid warehouse or exposed to the elements prior to purchase and for how long? Did they sit on a train in the rain or snow uncovered during transport and for how long? These are questions that should and can be answered ahead of time with some due diligence. Another way to prevent installation of moist building materials is to measure their moisture content with a commercially available moisture meter prior to installation. This can be a tedious process with the enormous amount of building materials needed for some projects, but by systematically measuring moisture content of these materials prior to installation as part of a Quality Assurance program can prevent mold growth and serious headaches after installation.
Another strategy for protecting building materials has emerged in recent years. According to Neil Tucker, with Seal All Shrink Wrap, his company has seen an uptick in their shrink-wrapping of construction materials business over the past five years. Mr. Tucker states that material engineers typically provide the specifications for the thickness and design of specific shrink wrap procedures. The most commonly used shrink wrap for commercial construction materials is 10 mil thickness resin material that has a protective life of approximately 12 months. Shrink wrapping can add more expense to the cost of construction but can be well worth the investment to prevent mold growth on building materials after installation.
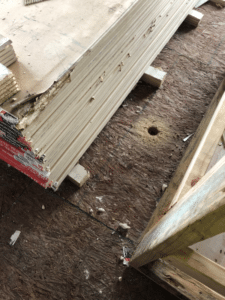
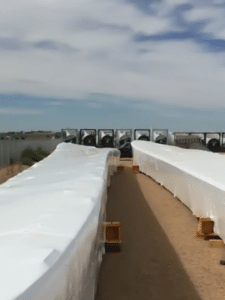
Left: Stored drywall, unprotected. Photo courtesy of Nacole Caputo with VERTEX
Right: Stored materials, Shrink-wrapped. Photo courtesy of Seal All Shrink Wrap LLC
Proactive Measures to Safeguard Construction Materials from Mold Growth
In summary, the following are some tips for protecting construction materials prior to installation with the intent of preventing mold growth after installation:
- Investigate construction materials purchased as to where and under what conditions they were/are stored (e.g. outdoors vs. indoors, humid environment vs. controlled environment) prior to purchase and delivery.
- Select building materials with anti-microbial properties.
- Collect moisture measurements of wood and cellulose-based building materials prior to installation and ensure they do not exhibit excess moisture. Be advised that this requires a knowledge base of what acceptable moisture content is in different types of building materials. Shrink-wrap or otherwise protect construction materials from top to bottom during transport and storage on site and ensure the integrity of shrink wrap is maintained until installation.
- Ensure that building materials to be installed are stored at least 4 inches off of the ground and that they do not come into direct contact with the ground or soils on the site.
- Ensure that construction materials are stored on a level surface and not down slope on site to prevent stormwater runoff from intruding and accumulating in the storage area(s).
- Ensure that the building envelopes, roofs, and crawlspaces are sealed to prevent moisture intrusion, either from stormwater or from seepage of moisture through concrete foundations.
- Ensure that concrete and gypcrete have cured and dried fully prior to installing framing and drywall to prevent trapping of moisture between the concrete and wall/ceiling members.
In conclusion, mold growth in new construction can have significant impacts on project costs, project schedules, and even possibly diminishing the market value of newly built structures. By protecting building materials from moisture from the early stages of off-site storage prior to purchase, through the transport and on-site storage stages, builders can prevent mold from growing in newly constructed buildings.
For more information on VERTEX Industrial Hygiene and Environmental Services, contact Thomas Koch, tkoch@vertexeng.com or send an email to info@vertexeng.com.
To learn more about VERTEX’s comprehensive AEC services or to speak with an Expert, call 888.298.5162 or submit an inquiry.
[1] Wood Handbook, US Department of Agriculture, Forest Service, Forest Products Laboratory, April 2010
[2] ASHRAE 62.1 Ventilation for Acceptable Indoor Air Quality, 2019