The use of natural materials as structural elements comes with related natural decay. Timber, for example, is composed of organic materials that make it a reliable source of energy that many organisms have evolved to take advantage of. Most of these organisms live on the forest floor where dead timber would naturally be found. The main difference between the environment of the forest floor and the environment inside of timber structures is the level of humidity, the amount of ventilation, and the environmental temperature.
Environmental conditions that facilitate natural decay are not comfortable for humans and as a result, the environmental conditions that are ideal for humans are less than ideal and unsuitable for wood decay organisms. However, the environments suitable for such organisms develop in timber structures due to building defects, inadequate ventilation, lack of maintenance or neglect, water penetration, and other factors. The building code attempts to address many of these factors and requires the use of preservative treated lumber in building conditions that may otherwise facilitate natural decay.
Code Requirements for Treated Lumber
Various sections of the International Residential Code (IRC) and the International Building Code (IBC) require the use of preservative treated lumber in applications where there is an increased likelihood of exposure to environmental conditions facilitating decay compared to normal dry use conditions. For example, Section 2304.12 of the 2021 IBC and Section R317.1 of the 2021 IRC require the use of naturally durable or preservative-treated wood where floor joists are located closer than 18-inches to exposed ground, where the wood members act as sill plates on concrete in direct contact with the ground, and in various other instances. These same sections in both the IRC and IBC explicitly state that when the requirements for preservative treated lumber are met, the wood must be preservative treated in accordance with Use Category U1 as defined by the American Wood Protection Association (AWPA).
AWPA Use Category System
The AWPA Use Category System (UCS) designates the preservative systems that have been determined to be effective in protecting wood products under specified exposure conditions such as those listed in the IBC and IRC. AWPA UCS U1 defines the following five different use cases:
- Use Category 1 – Interior/Dry
- Use Category 2 – Interior/Damp
- Use Category 3 – Above Ground
- Use Category 4 – Ground Contact
- Use Category 5 – Marine Use
With respect to structural systems, Use Category 2 is the most common in typical Colorado based residential construction and is defined as materials used for interior construction not in contact with the ground that may be subject to dampness such as floor framing and sill plates. Use Categories 3 and 4 are rare but can become applicable in situations where wood sheathing is not covered by a weather resistive barrier, wood foundations are used, or sill plates are located closer than six inches to finished grade. Use Categories 1 and 5 are almost never applicable to residential structural components.
The remainder of this article focuses on Use Category 2 for which the most common deterioration agents are decay fungi and insects with a low chance of biodeterioration for which there are several preservative treatments approved by the AWPA and permitted for use by the IRC and IBC. While some of the approved treatments leave behind physical indicators that the wood has been treated (i.e. texture and coloration), not all do. Accordingly, Section R317.2 of the 2021 IRC and Section 2303.1.9.1 of the 2021 IBC require that preservative treated lumber bear a quality mark (see Figure 1) by way of stamp or affixed label that identifies the following:
- Treatment plant/manufacture
- Type of preservative used
- Minimum preservation retention
- End use for which the product was treated
- AWPA standard for which the product was treated
- Identity of the accredited inspection agency that maintains continuous supervision and testing of the treated products
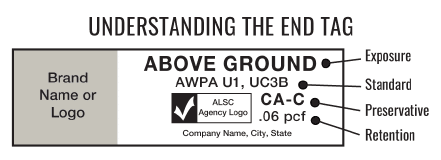
Intent of the Code Requirements and Practices that Result in Construction Claims
The intent behind the various code requirements is clear: they aim to prevent the appearance of wood decay organisms. Common construction defects that promote wood decay include:
- Defective flashings
- Uncapped out-of-service chimneys
- Missing roof tiles
- Blocked gutters that allow the accumulation of moisture
- Lack of ventilation
- The absence of moisture barriers
- Failure to install preservative treated lumber when required
Building defects such as the aforementioned examples increase the moisture contents which give rise to fungal decay organisms like Dry Rot, Wet Rot, Soft Rot, Mold, and Bacteria. Any timber with a moisture content over 19% is considered to be susceptible to fungal decay, but the organisms growth rate is dependent on higher moisture contents.
For example, Dry Rot grows at an “optimum rate when it is between 30 and 40%” while Wet Rot “needs and optimum moisture content of 50-60%” (Singh and White, 5). Similar to fungal decay, wood-boring insects that use timber as a food source such as termites generally only attack damp wood.
The Missing Quality Mark Issue
As mentioned earlier, when lumber can be exposed to moist environmental conditions, the building code requires preservative treated lumber to be used. The code requirements also state that preservative treated wood products bear quality marks identifying they are preservative treated in accordance with AWPA UCS U1. Construction claims often arise out of the lack of this required identifying mark.
This construction defect claim is becoming more common in situations where preservative treated lumber is used but bears no quality mark.
This most often happens at Use Category 2 places in a building, such as with wood framed structural floors over crawl spaces. The framing members are more likely to be subject to intermittent dampness, however, the treated lumber bears no stamp or preservative treated identifier on the exposed faces. This often occurs because the quality marks are usually affixed to the end of wood members as illustrated in Figure 2. In order to facilitate installation of floor joists and finishes, these labels are typically removed prior to installation or made inaccessible to view due to the fact that the ends of joists are not visible in typical conditions.
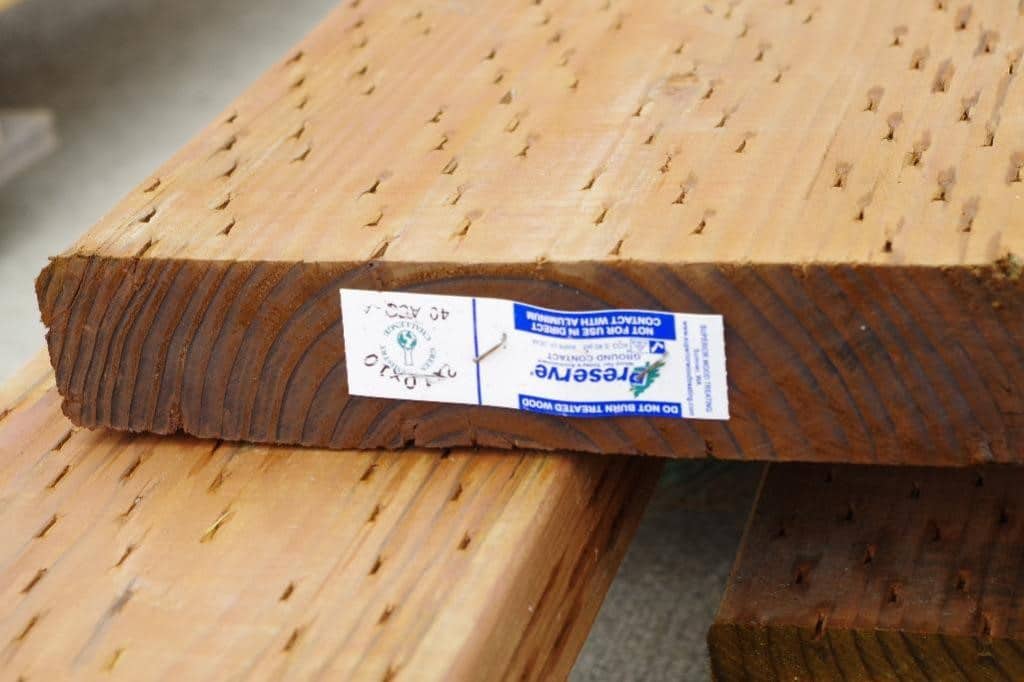
Case Study of a Construction Defect Claim involving Treated Wood
Vertex was contracted to evaluate claims made by an engineering expert hired by the owner of a single-family residential structure in Colorado against the home builder. The foundation system of the single-family structure consisted of 8-inch-wide reinforced concrete grade beams supported by drilled piers which in turn supported a structural floor at the basement level. The basement floor was a structurally supported joist and beam system supported on interior wide flange steel beams and by a wood ledger bolted to the concrete grade beams at the perimeter.
The original structural plans called for the wood joists to be affixed to a steel ledger rather than a wood ledger and the engineering professional hired by the homeowner took issue with this discrepancy. The issue taken was associated with concern that the member in direct contact with concrete was not preservative treated and subject to higher risk of natural decay. The engineering expert was critical of the fact that neither the floor joists nor the wood ledger bore a stamp or other indicator declaring that the joists were preservative treated. Therefore, the expert cited sections R317.1.1 and R317.1.2 of the 2012 IRC stating that wood members in direct contact with concrete and within 18-inches of the crawlspace grade are required to be preservative treated.
During site inspections of the home, VERTEX’s construction experts confirmed that neither the wood joists nor the wood ledger bore a stamp or label indicating that the floor joists were preservative treated; however, other visual indicators of preservative treatment were observed. In this instance, a red tint consistent with ACQ preservative treatment was observable and our office was able to successfully demonstrate the as-built condition was code compliant resulting in a favorable settlement for our client.
VERTEX HAS YOU COVERED
In situations where documentation and visual inspection are unable to definitively confirm the presence of preservative treated lumber, testing agencies can determine if lumber is preservative treated. In circumstances like this, VERTEX’s forensic team can work with an accredited testing agency and the involved parties to coordinate the removal, packaging, and delivery of samples for laboratory testing. Finally, contractors can help protect themselves from claims such as these by removing and reaffixing labels to viewable locations and maintaining invoices, purchase orders and other documentation to demonstrate the lumber purchased and installed is in fact preservative treated.
To learn more about VERTEX’s Forensic & Construction Claim Services, or to speak with a Forensic Expert, visit our services area, call 888.298.5162 or submit an inquiry.
Author: Xavier Montoya