Introduction to HEPA Filter Integrity Testing
High Efficiency Particulate Air (HEPA) filtration represents a critical component in maintaining state of control within sterile compounding facilities and controlled environments. HEPA filters are strategically deployed throughout Sterile Compounding Facilities, including Secondary Engineering Controls (SEC) and Primary Engineering Controls (PEC). The fundamental function of these filters—removing particles from air entering controlled environments—requires meticulous verification through properly executed integrity testing.
The Technical Challenges of HEPA Leak Detection
A leak in a HEPA filter is technically defined as a penetration greater than 0.01% of the upstream challenge. Detecting such leaks presents significant technical challenges due to their microscopic nature. Unlike common pressure vessel leaks that produce audible or visible indicators, HEPA filter leaks exist at the particulate level, beyond direct sensory detection. This necessitates specialized instrumentation and methodologies for accurate assessment.
Technical Requirements for Effective HEPA Filter Integrity Testing
HEPA filter integrity testing requires three essential technical components to ensure repeatable and accurate results:
- Appropriate Airflow: The HEPA filter requires adequate airflow during testing. The volume of airflow directly correlates with the upstream concentration requirements—higher airflow necessitates proportionally more aerosol to achieve the minimum upstream concentration of 10 µg/L.
- Upstream Aerosol Challenge: Creating a properly distributed upstream challenge using an aerosol generator represents one of the most technically demanding aspects of the test. This often becomes challenging due to design limitations in aerosol injection systems.
- Accurate Concentration Measurement: An upstream concentration measurement is required to calibrate the Aerosol Photometer relative to the aerosol concentration injected upstream of the HEPA filter. This can be accomplished through two methodologies:
- Measured upstream concentration (preferred methodology)
- Calculated upstream concentration (alternative methodology when measurement is not feasible)
Industry Standards for Documentation
According to CETA CAG-008 Certification Matrix for Sterile and Nonsterile USP Compounding Facilities, comprehensive documentation for each HEPA filter under test should include:
- Aerosol injection location and methodology
- Upstream concentration measurement location and technique (measured vs. calculated)
- Upstream concentration value for each HEPA filter
- Detailed filter diagram with indication of any leaks found and subsequent repairs
- Percent penetration for each identified filter leak
- Statement confirming no leaks exceeding the maximum allowable 0.01% were detected
- Pass/fail determination for each HEPA filter
Figure 1: An ATI 2I aerosol photometer and an ATI 6D Laskin Nozzle Generator.
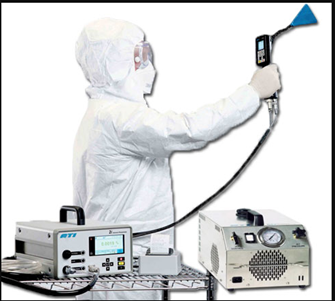
Advanced Documentation Protocols
Comprehensive documentation provides significant technical advantages beyond regulatory compliance. An advanced HEPA Filter Leak Test Report should document:
- Filter location with corresponding identification system
- Filter specification (type, dimensions)
- Operational parameters (CFM, Static Pressure)
- Upstream aerosol concentration with measurement methodology
- Number of Laskin Nozzles utilized
- As-found and as-left leak penetration measurements
- Classification of leak type (media, gasket, frame)
- Repair specifications (patch dimensions, materials)
- Detailed documentation of aerosol injection methodology
Technical Significance of Comprehensive Data Collection
Airflow and Pressure Documentation
Recording Cubic Feet per Minute (CFM) and static pressure measurements during integrity testing provides critical trending data with multiple technical applications:
- Correlation with Upstream Concentration: Airflow volume directly impacts the upstream concentration. A significant change in airflow between certifications may result in variations in concentration values, potentially affecting test validity.
- Filter Loading Assessment: Static pressure readings provide quantitative data regarding filter loading over time. The correlation between static pressure and CFM allows for evidence-based determination of filter replacement requirements:
- Decreased CFM with decreased static pressure suggests system airflow issues
- Decreased CFM with increased static pressure indicates progressive filter loading
This data-driven approach prevents unnecessary filter replacements while ensuring timely intervention when required.
Upstream Concentration Measurement Methodology
CETA CAG-003 Certification of Sterile Compounding Facilities for USP Compliance specifies that measured upstream concentration is preferred whenever technically feasible. Documenting whether the concentration was measured or calculated provides critical context:
- Verification of Proper Aerosol Distribution: Measured concentrations confirm that the aerosol injection system is delivering challenge material to the intended filter.
- Detection of Installation Anomalies: Measurement can identify aerosol delivery system installation errors, such as cross-connected injection ports or misdirected aerosol paths.
- Precision and Accuracy: Direct measurement provides actual concentration values rather than theoretical calculations, increasing test validity.
In scenarios where measurement is not technically feasible, comprehensive documentation should include the justification for calculation, the specific calculation methodology employed, and the parameters used to ensure repeatability.
Leak Characterization and Remediation
Detailed documentation of leak characteristics provides critical technical information:
- Source Identification: Classifying leaks as media, gasket, or frame related allows for identification of manufacturing defects, seal degradation, or handling damage.
- Contamination Risk Assessment: Leak magnitude and location data can correlate with environmental monitoring results to identify potential contamination pathways.
- Repair Documentation: Recording patch dimensions ensures compliance with repair limitations (maximum 3% of filter face area with no single repair exceeding 1.5″ in lesser dimension).
Aerosol Injection Specifications
Comprehensive documentation of aerosol injection methodology represents a critical element for ensuring test repeatability:
- Port Specifications: Documentation should include physical specifications (¼”, ½”, ¾”, NPT thread, quick connect, barbed fitting).
- Injection Location: Precise documentation of injection location (manufacturer port on filter frame, remote ceiling port, external room location).
- Measurement Point: Specific documentation of upstream concentration measurement location, particularly when multiple potential sampling points exist.
Figure 2: Remote aerosol injection system with ½” NPT room side port.
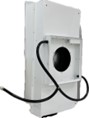
This technical specificity ensures consistency across multiple testing cycles, even when performed by different certification personnel.
Conclusion
HEPA filter integrity testing represents a technically complex procedure requiring specialized methodologies and instrumentation. Comprehensive documentation serves multiple technical objectives beyond basic compliance, including:
- Ensuring technical repeatability across certification cycles
- Facilitating evidence-based filter maintenance decisions
- Providing data correlation for environmental monitoring investigations
- Establishing technical justification for testing methodologies
By advancing documentation standards beyond minimum requirements, facilities can enhance operational efficiency, reduce unnecessary downtime, and strengthen contamination control strategies through data-driven decision making. This approach supports the pharmaceutical industry’s fundamental obligation to ensure product safety through rigorous, defensible technical processes.
VERTEX supports pharmaceutical and healthcare clients with expert services in Industrial Hygiene, Indoor Air Quality, and Environmental Compliance. Our specialists deliver practical, defensible solutions to ensure safety, compliance, and performance in critical environments.
Contact VERTEX today to learn how we can support your facility.
Authored by Jacob Warden, Senior Consultant – IHBS, Compliance & Regulatory Services