COVID-19 Disrupts Supply Chains Causing Construction Delays
From the onset of the COVID-19 pandemic, many feared that the virus would have a powerful impact on supply chains, resulting in construction delays.
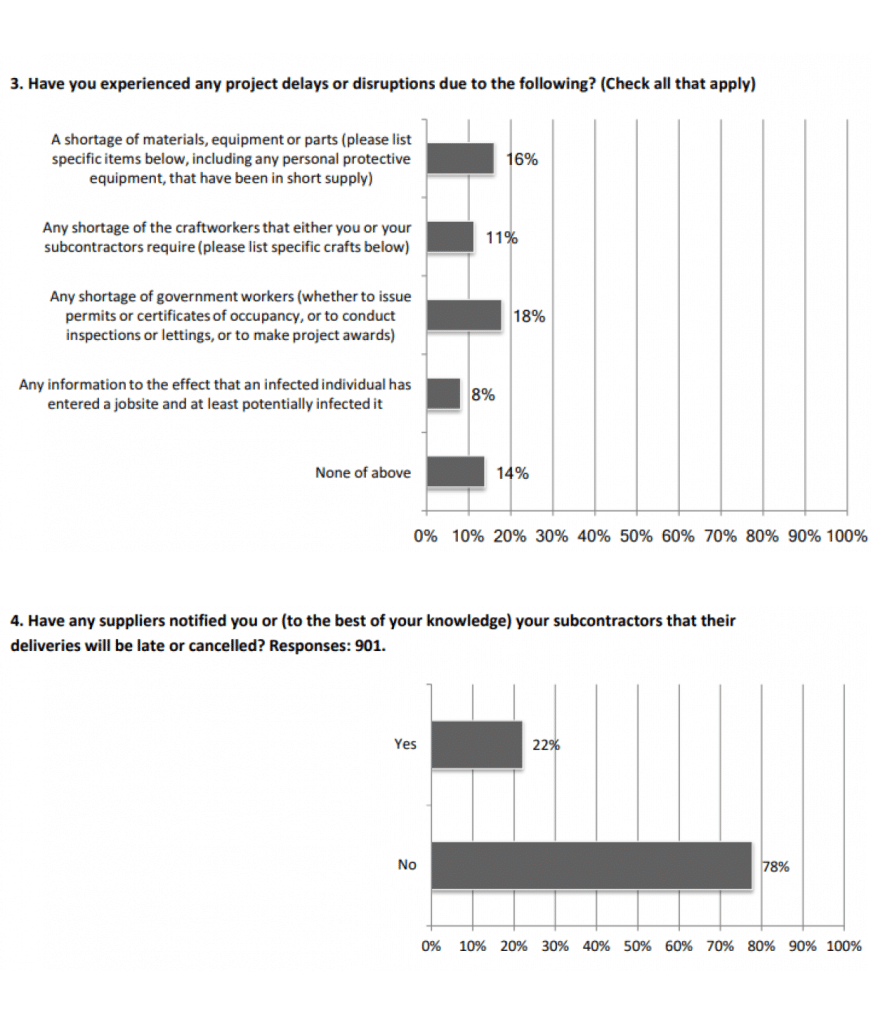
Associated General Contractors of America (AGC) recently published the results of survey poll questions taken from March 17 – 19, 2020. When asked if suppliers notified contractors or their subcontractors that deliveries would be late or canceled, 22%, or 198 of 901 respondents, indicated they were made aware of supply-chain delays. Additionally, 16% of respondents answered affirmatively they had experienced project delays or disruptions resulting from a shortage of materials, equipment, or parts (which could include a shortage of PPE, such as respirators). AGC has begun polling for a subsequent edition of the survey to track how these figures have changed – once these results are released, we will update this post accordingly.
In many states and municipalities, construction has been deemed an “essential” function; however, manufacturing plants and trucking companies may not be operating to serve the industry’s needs, and a diminishing workforce due to symptomatic employees, care for family members, or the possibility of infection increases the potential for absenteeism across all industries.
Evaluation of Remaining Work
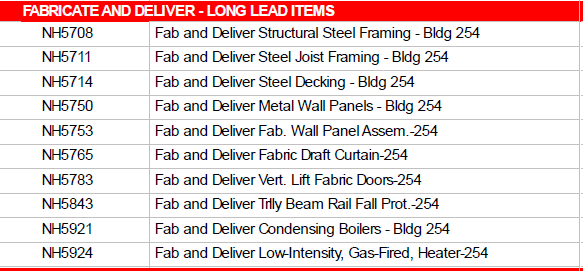
Contractors should perform a thorough review of materials and equipment which have not yet been delivered to a project. This evaluation should identify the manufacturers involved, and where materials are sourced and manufactured to understand potential risks. In anticipation of supply chain delays, contractors should review their schedules to ensure there are material delivery activities in the schedule. Contractors should also review their insurance policies as they relate to business disruption and supply chain insurance. VERTEX has spoken to several suppliers and distributors who have advised they are a part of daily calls with manufacturers. Through discussions with suppliers, contractors should inquire if there are any parts or goods which are incorporated into a final product that could impact the delivery of the final product. For example, electronic hardware fabricated in the United States may likely use electronic components sourced from China. With many construction materials and specialty equipment manufactured in China, a wave of diminished supply may not have hit fully yet as a result of shutdowns in China, although China is expected to ramp up production as the virus comes under control.
A contingency plan should be evaluated for critical materials for potential alternative sources. For Federal contracts, FAR 52-249-8(d) states “if the failure to perform is caused by the default of a subcontractor at any tier, and if the cause of the default is beyond the control of both the Contractor and subcontractor, and without the fault or negligence of either, the Contractor shall not be liable for any excess costs for failure to perform, unless the subcontracted supplies or services were obtainable from other sources in sufficient time for the Contractor to meet the required delivery schedule.” Thus, contractors should document their efforts to identify potential alternatives and how a substitution could impact the work and the schedule.
Not only should contractors review materials needed for the project internally and with their subcontractors, but the Owner should be consulted as well if they are supplying any material or Furniture, Fixtures, and Equipment (FF&E).
Materials incorporated into the work are not the only items that should be considered. Many contractors are finding that just because construction is continuing, external factors are still causing delays, such as the shutdown of state or local inspections, or inability to pull or renew permits. Similarly, there are materials and equipment needed to perform work that could also be unavailable, such as temporary hoists; cranes and derricks; testing equipment for Commissioning, Start-up and Testing & Balancing; and more.
Relevant Contract Provisions and Schedule/Cost Recovery
If a contractor becomes aware of a supply chain disruption or unavailability of materials, they should promptly provide notice to the Owner. VERTEX recommends working with counsel to review contract provisions and develop notices accordingly.
Per §8.3.1 of the AIA A201:
If the Contractor is delayed at any time in the commencement or progress of the Work by (1) an act of neglect of the Owner or Architect, of an employee of either, or of a Separate Contractor; (2) by changes ordered in the Work; (3) by labor disputes, fire, unusual delay in deliveries, unavoidable casualties; adverse weather conditions documented in accordance with Section 15.1.6.2, or other causes beyond the Contractor’s control; (4) by delay authorized by the Owner pending mediation and binding dispute resolution; or (5) by other causes that the Contractor asserts, and the Architect determines, justify delay, then the Contract Time shall be extended for such reasonable time as the Architect may determine. [emphasis added]
Per the FAR, contractors are protected in §52.249-10 Default against a default from delays “arising from unforeseeable causes beyond the control and without the fault or negligence of the contractor,” including “epidemics,” “quarantine restrictions,” and “delays of subcontractors or suppliers at any tier arising from unforeseeable causes beyond the control and without the fault or negligence of both the contractor and the subcontractors or suppliers.” Within 10 days of the beginning of any delay, the contractor must notify the Contracting Officer in writing of the causes of the delay.
FAR §52.249-14 Excusable Delays reinforces §52.249-10, and both clauses provide a potential avenue for relief of an excusable delay if the delay is in fact related to COVID-19 – a global pandemic, a potential government-mandated quarantine restriction, and/or the delay to the contractor’s subcontractors or suppliers that was unforeseeable and outside of their control. The determination of an excusable delay under this clause would result in an extension of time, but no cost relief. FAR §52.243-1 through -4 Changes may provide an avenue for cost and schedule relief if the Government directs performance (or non-performance) – this clause is typically triggered when a contractor received a specific direction from the Contracting Officer. Again, VERTEX recommends contractors review their specific contracts with counsel.
In these circumstances, a time extension should not be taken for granted and would require substantiation of the delay, and justification through a schedule analysis to demonstrate a delay to the critical path. Contractors who prepare frequent, reliable schedule updates, with proper detail and compliant with contract requirements, are well-positioned for a schedule analysis. Others may require schedule maintenance or demonstration of the delay using alternative practices. Concurrency with other delays should also be evaluated, although a non-compensable time extension can still be issued if COVID-19 excusable delays are concurrent with contractor delays.
VERTEX frequently performs schedule/delay analyses, productivity impact claims, damage analyses, schedule generation and maintenance, preparation of notices, and other advisory services. VERTEX can assist contractors in addressing these impacts and preparing claims or advising Owners in the evaluation of claims.
Other Construction Delay Considerations
Consideration needs to be given if an alternative product or material is to be used to mitigate a supply chain disruption. As with all substitutions, the contractor needs to make sure the product meets the requirements of the contract. Any deviations from the requirements should be clearly indicated as part of a submittal process of the product (ref. FAR 52.236-21; UFGS 01 33 00; AIA A201 §3.12.8 – 9). It is likely there may be price differentials associated with a substitution, or credits required from suppliers and/or subcontractors contracted to provide the material which is unavailable. Contractors can rely on their subcontractors and suppliers to manage these risks but should nonetheless provide notice and a change request prior to proceeding with a substitution if there are additional costs involved that the contractor is seeking compensation for. Contractors should also contemplate the availability of manufacturer’s representatives when sourcing materials. Commercial impracticability may rule out some substitutions.
Lastly, contractors who are impacted by delays associated with delivery should carefully evaluate efforts to compensate for or work around these issues. Some contractors may consider pacing their work or performing out-of-sequencing work. Pacing is a conscious and contemporaneous decision to temper the progress of an activity against another activity experiencing a delay due to an independent cause. For pacing considerations, contractors must know their schedule, their available float and understand float ownership on the project before considering pacing. It is critical a contractor document its resource management to justify its decisions. In the absence of certain materials, contractors may elect to perform work out-of-sequence. There are a number of factors to consider, such as project conditions (are temperature, humidity, and moisture requirements met?), impact on other trades (can starting an activity early or out-of-sequence create inefficiencies?), and constructability. Making these decisions collectively, with subcontractors and the Owner, can improve the potential for recovery or identify potential constraints. Open communication, especially as it relates to cost, is important when making decisions to work around impacts. Overdocumentation and abundance of notice is always a recommended practice during these turbulent times.
To learn more about VERTEX’s Construction Claims Consulting or to speak with a Construction Claims Expert, call 888.298.5162 or submit an inquiry.