Components of a Gasoline Station
A gasoline station is typically comprised of a convenience store and fueling system. Sometimes, but not always, a gasoline station can include a car wash and/or a quick service restaurant as well as auto repair services. The fueling system is typically comprised of a fueling canopy, dispensers, underground storage tanks (USTs), product lines, Veeder Root system (automatic tank gauging system), emergency shut offs, monitoring wells, and vent pipes.
Common Sources and Causes of Releases at Gasoline Stations
So, what causes environmental pollution conditions at gas stations? Malfunctions of the fueling system are generally to blame. According to the United States Environmental Protection Agency (EPA), some common vulnerable areas include the bottom of USTs (especially underneath the manhole where gauging sticks are or were formerly used), associated piping, UST fill manholes, and dispensers.
The product lines and fittings are what brings the petroleum from the UST to the dispensers. If the product lines are steel, it should be noted that the steel could be subject to corrosion. During UST removals, staining indicative of past releases can be observed, especially near fittings. Newer product lines are generally constructed of double walled fiberglass and the interstice is electronically monitored for leaks. There are also leak detectors which monitor fluid pressure, which will shut down the flow of product in the event of a leak.
Tank overfills can occur when a truck delivers product to a UST. If the UST becomes full, there should be an emergency shut off device to stop the flow of the petroleum product; however, it’s not unusual for some overflow to spill onto the ground around the fill port where the hose was disconnected. The fill ports are typically inserted through the spill buckets. In the event of a small spill, the product is generally captured in the spill buckets, and there is also a drain valve that can be opened so the overfilled product can flow back into the UST. During delivery, there are other places for error including dispensing into the wrong fill port or insecure hose connections.
Dispensers have multiple fittings and hose connections, which is another place leaks can occur. Older dispensers have typically been constructed above soil and therefore any leaks will go directly to the ground surface and newer dispensers typically are constructed over spill containment, which will catch any of those leaks and drips over time.
Prior to 1980, USTs were typically constructed as steel, which can corrode, resulting in holes in the USTs. New USTs are generally required to be constructed of double-walled fiberglass and/or consist of cathodic protection systems to prevent corrosion.
The diagram below shows the different components that make up a UST and areas where the releases generally come from.
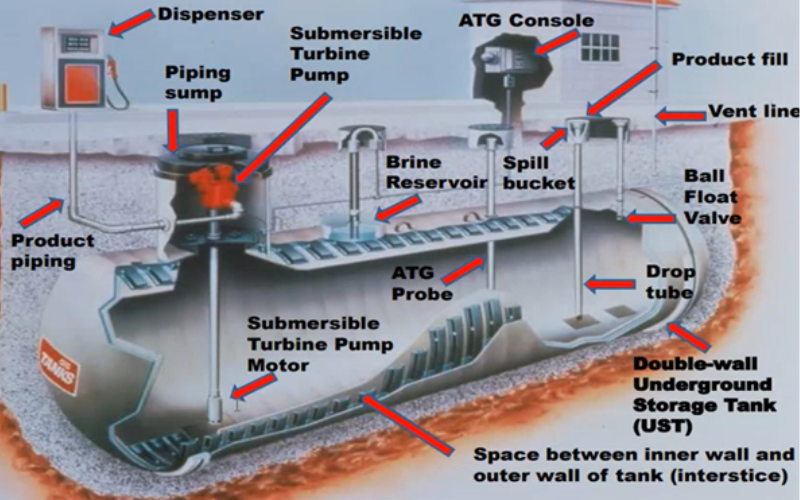
Image source: www.nistm.org
Fueling System Release Detection and Protection
Fueling systems at a gasoline station are typically equipped with release detection, spill protection, and overfill protection. The release detection equipment and methods typically include automatic tank gauging (ATG) systems, vapor monitoring, groundwater monitoring, statistical inventory reconciliation (SIR), manual tank gauging, tank tightness testing, and interstitial monitoring.
ATG systems are typically seen as Veeder Roots within the convenience store. Daily print outs from the ATG system will show the status and include fuel level monitoring. These print outs should be documented by the gasoline station staff on a daily basis.
Vapor monitoring is a method that samples either product vapors in the soil gas or presence of a tracer compound introduced into the UST system. Vapor monitoring systems have permanently installed equipment to continuously or periodically gather and analyze vapor samples and respond to a release with a visual or audible alarm.
Groundwater monitoring involves the use of permanent monitoring wells placed close to the USTs. The wells are checked on a regular basis for the presence of product that may have leaked from the UST and is floating on the groundwater. The components of a groundwater monitoring system include the monitoring well (2-4 inches in diameter) and the monitoring device. Detection devices may be permanently installed in the well for continuous detection of leaked product.
SIR analyzes inventory, delivery, and dispensing data collected over time to determine whether the fueling system is leaking. Each day the product level is measured using a gauge stick or other tank level monitor. All withdrawal records from the UST and all deliveries to the UST are kept and provided to SIR vendor. The SIR vendor then conducts a statistical analysis of the data to determine whether a leak has occurred.
Manual tank gauging requires keeping the UST undisturbed for at least 36 hours before measuring the contents and it should be conducted each week. Manual tank gauging can be used as the sole method of leak detection for the life of the UST only for USTs up to 1,000-gallons. USTs greater than 1,000-gallons can use this method in combination with tank tightness testing.
Tank tightness testing and inventory control is typically conducted every 3 years. Many tightness test methods are volumetric methods in which the change in product level in a tank over several hours is measured very precisely.
Interstitial monitoring detects leaks in the space between the UST and a second barrier (secondary containment) where any leaked product accumulates. Interstitial monitors are used to check the area between the tank and the barrier for leaks. The monitors can be automated systems or as simple as a dipstick.
How Can VERTEX Help?
Whether it be due diligence reporting and investigations, remedial projects, or insurance claim support, our experienced team of Environmental Professionals at VERTEX can assist in identifying and managing petroleum releases from gasoline stations as well as cleanup/remediation of identified petroleum releases. For more information or to learn more about VERTEX’s environmental and insurance support services or to speak with an Expert, call 888.298.5162 or submit an inquiry.